Corrosion Prevention
Pipeline corrosion
Pipeline corrosion is a natural occurrence.
Pipe material and essential properties deteriorate over time. Corrosion occurs due to electrochemical reactions of pipeline materials with their environment. You can find corrosion on the inside as well as outside surfaces. Like any other natural hazard, pipeline corrosion can cause a life-threatening failure. It can also cause expensive damage to the pipeline and related systems.
Corrosion is an electrochemical phenomenon in which a metal is naturally changing its composition to return to the low-energy oxide state – otherwise known as rusting. The basic chemical process is that an electric current will flow from the metal atoms in the pipeline, through ions in the surrounding soil or water and cause chemical changes to occur in the metal. This current is set up by the fundamental properties of the mixed elements in the presence of a charge conductor (the ground or water), and the atoms that will reduce the metal (the air which has oxygen).
Cathodic protection against corrosion
You can shield steel piping with cathodic protection to prevent corrosion. This technique reduces the corrosion of the metal surface. It does so by making the surface the cathode of an electrochemical cell. This cathodic protection system works by applying a small current to the pipeline.
It operates by passing direct current, opposite to the corrosion current, continuously from electrodes (anodes) which are installed in the soil or water surrounding the structure to be protected. The corrosion is stopped when the protection current is of sufficient magnitude and is properly distributed to offset the intrinsic chemically derived current. Although the corrosion current is based on thermodynamics and occurs automatically, the protection current requires an external power source. This is where a microgrid would come into play.
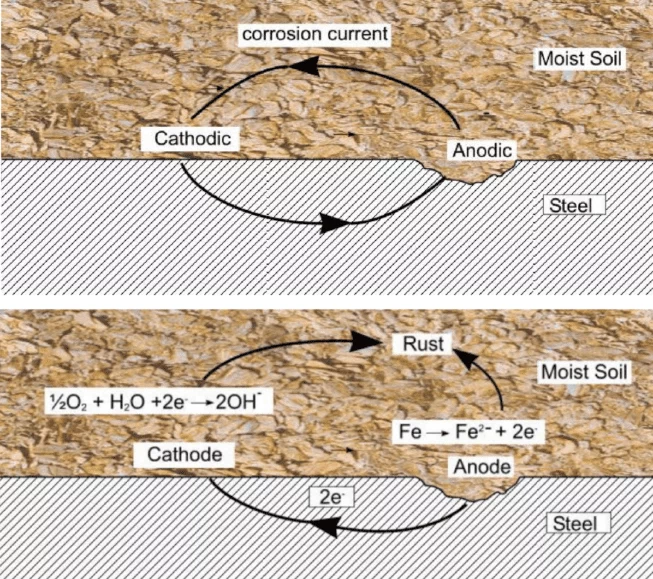
The principle of cathodic protection prevents this natural process from occurring.
Corrosion of buried metal structures is mainly dependent on the soil composition, resistivity, pH, water and oxygen content, etc. The most aggressive soil types are clays, mixed clays, muds and sands with high salinity. The most severe corrosion effects can occur on a pipe that passes through soils of different compositions. Traditionally, corrosion prevention of underground pipelines has been done by coatings (bitumen, coal tar and epoxy powder or polyethylene) or applied tapes. However, in corrosive environments coatings or tapes cannot totally prevent corrosion because of porosity caused during their manufacturing, transportation or installation. Therefore, although the standard less expensive up-front approach will reduce the corrosion effects, they only reduce. They do not stop the problem and the pipes will eventually need to be dug up.
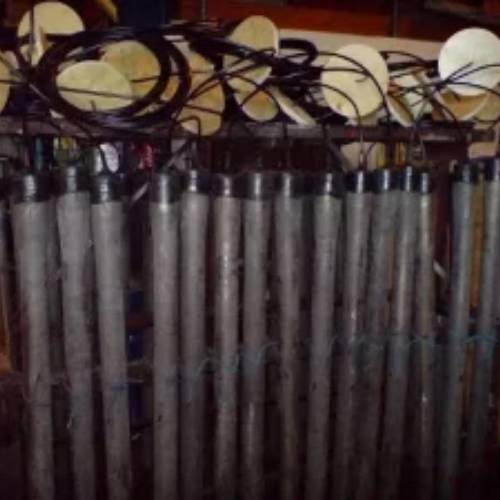
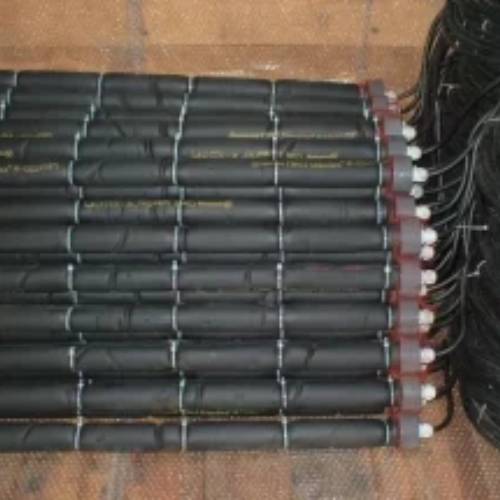
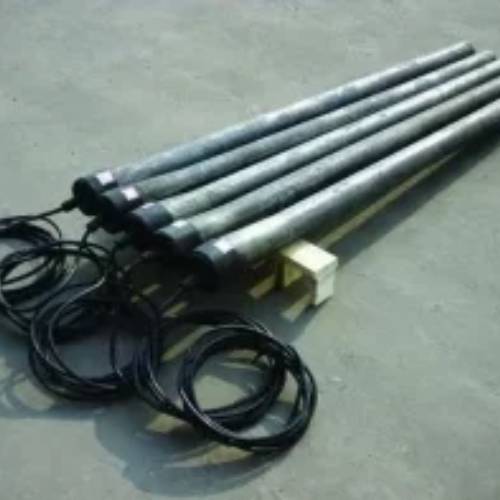
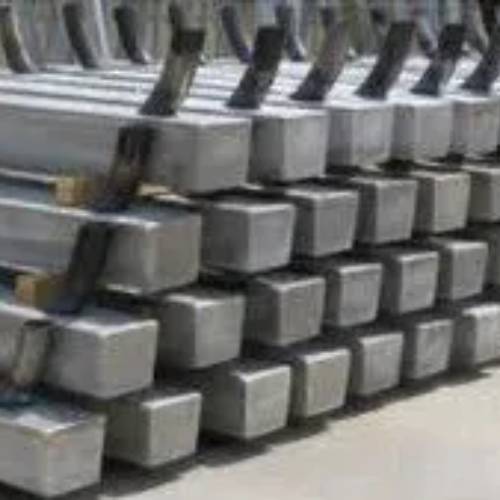
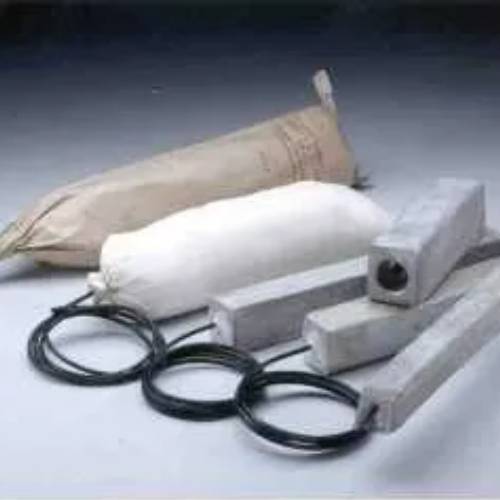
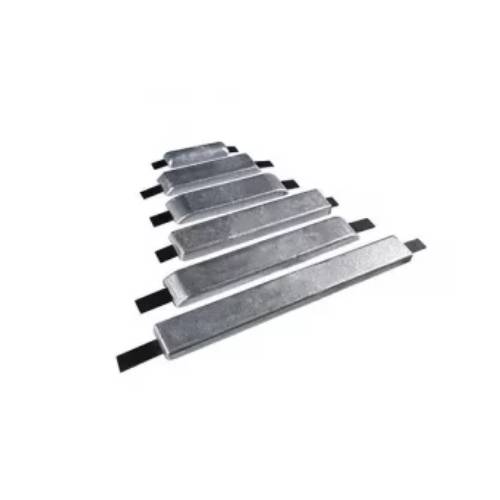
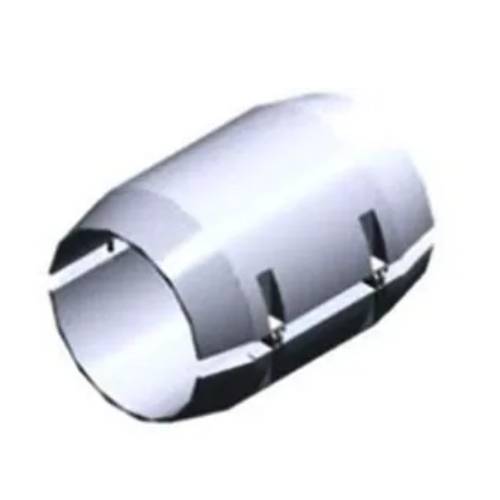
Anodes
Australian Mining Product and Services supplies all types of sacrificial anodes – standard or customised
Galvanic Anode (Sacrificial Anode)
A galvanic anode is the main component of a galvanic cathodic protection system used to protect buried or submerged metallic structures from corrosion. They are made from a metal alloy with a more “active” voltage (more negative reduction potential / more positive electrochemical potential) than the metal of the structure. The difference in potential between the two metals means that the galvanic anode corrodes so that the anode material is consumed in preference to the structure.
The loss (or sacrifice) of the anode material gives rise to the alternative name of sacrificial anode.
There are three main metals used as galvanic anodes, Magnesium, Aluminium and Zinc.
They are all available as blocks, rods, plates or extruded ribbon. Each material has advantages and disadvantages and is made for different purposes.
Application
Anodes for ICCP systems are available in a variety of shapes and sizes.
Common anodes are tubular and solid rod shapes or continuous ribbons of various materials. These include high silicon cast iron, graphite, mixed metal oxide, platinum and niobium coated wire and other materials
Dimensionally Stable Anodes (DSA)
Normally, Electrodes (Anodes) consist of a basic component, which is responsible for mechanical stability and uniform current distribution. As Titanium has all these characteristics, insoluble electrodes are manufactured with titanium as a basic component.
The excellent stability of mixed metal oxide-coated titanium anodes have been used for almost 30 years. Mixed Metal Oxide-coated titanium anodes are used in various environments such as seawater, brackish water, freshwater, carbon backfill, and concrete.
Many structure owners and corrosion control engineers use Mixed Metal Oxides and coated titanium anodes only specify the sizes without understanding the characteristics, limitations and evaluation method of the anodes. There are many different size and shapes are available, wire, ribbon, mesh, expanded mesh, rod, tubular, disc, probe etc.
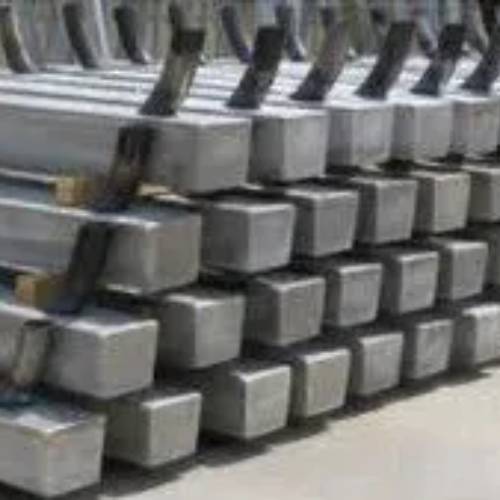
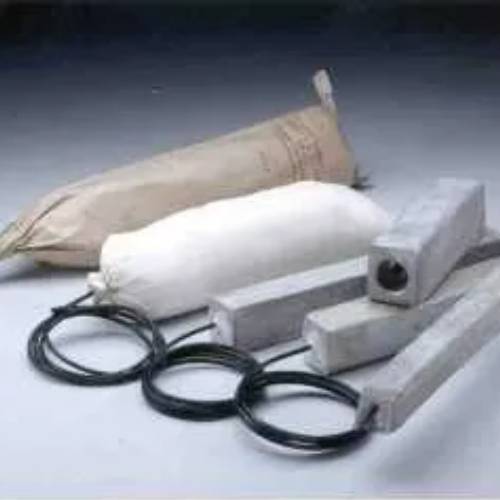
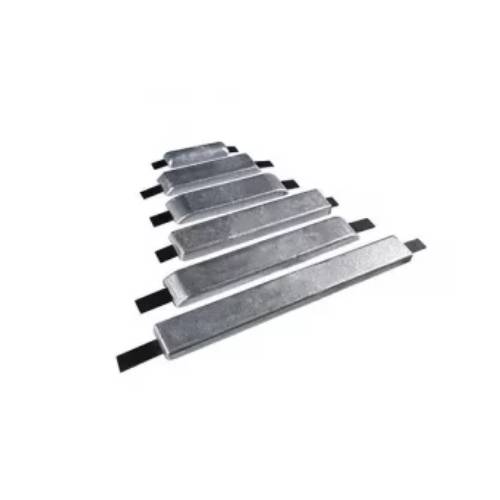
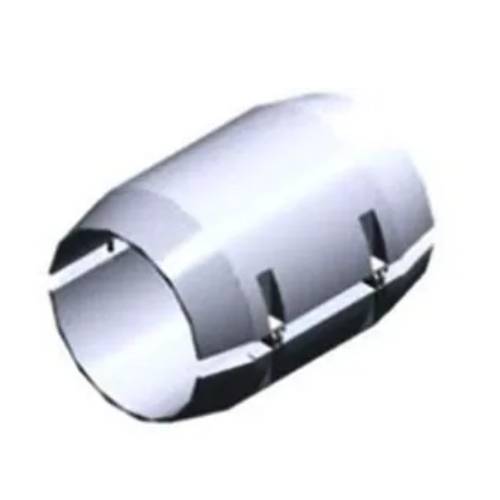
Corrosion Protection Junction Box /Test Posts
Application
Cathodic protection junction boxes are designed to provide a termination point anode cables, cathode (structure) cables, structure sense cable, reference electrode cables before routing to a cathodic protection rectifiers.
These junction boxes generally made of metallic or non-metallic materials. Many cases these boxes are coated with powder coating as per their location of use.
Junction boxes for positive and negative current distribution and control , and for resistance bonding are available to meet exact client specifications. Suitable for onshore and marine environments in safe and hazardous areas.
When specifying a Cathodic Protection Junction Box assembly please clarify specific hardware and components required.
Type of Enclosure: Stainless Steel 316L & 304, Aluminium Explosion Proof, Painted Mild Steel Plastic GRP, Galvanized and Painted Cast Iron Custom Finishes, Please also specify IP, NEMA or Hazardous area classification requirement.
Explosion-Proof Junction Box
Internal Components: Resistors, Metering, Diodes, Shunts Monitoring, Labeling, Copper Links Terminals, unidirectional blocking diodes etc.
Mounting Options & Security: Support Frames, Security / Locking, Pole mount channel, Wall mount tabs or Customer Specified….
Non-Metallic Junction Box
Cathodic Protection Cables
Application
The quality of the cable is extremely important for the efficiency of cathodic protection system, specially the anode cables.
Commonly use cathodic protection cables are PVC/PVC, PE/PVC, EPR/CSP, XLPE/PVC, XLPE/PVC/SWA/PVC, PVDF/HMWPE/ PVC/ Nylon/ PVC. PE/ Nylon/ PE.
Cables used for cathodic protection systems must be highly corrosion resistant and capable of withstanding adverse environments to which they are exposed to on a consistent basis. High Molecular Weight Polyethylene (HMWPE) is suitable for most environments.
In saline environment, we recommend KYNAR/HMWPE or HALAR/HMWPE cables, which are dual extruded highly chlorine resistant power cables. Australian Mining Product and Services supplies all types of cables used in cathodic protection system.
HMWPE Cable for Cathodic Protection: High Molecular Weight Polyethylene (HMW-PE).
Cathodic Protection Cables: 600 Volts, Single Conductor, Stranded Copper. Stranded copper conductor conforms to ASTM Specification B-8. Insulation is high molecular weight polyethylene conforming to ASTM D-1248, Type 1, Class A, Category 5, Grades E4 & E5. Tensile Strengths Jl, J3.
Available with high-density polyethylene (Types II, III, IV) Class B & C (all colours).
Application: A direct burial DC cable for use in cathodic protection applications such as anode lead wires, header cables, structure connections, test leads and more.
The product can also be used for submerged installations in water tanks, offshore structures and other similar applications.
The polyethylene insulation is durable, abrasion resistant and flexible but has temperature and chemical limitations.
Halar/HMWPE Cable: Cathodic Protection Cables, Primary Halar Insulation, HMW (High Molecular Weight) Polyethylene Jacket.
Stranded bare copper conductor conforms to ASTM Specification B-8. An insulation of homogeneous wall of natural ECTFE fluoropolymer (Halar) shall be extruded over the conductor, jacket insulation is high molecular weight polyethylene conforming to ASTM-D-1248, Type 1, Class A, Category 5, Grades E4 and E5. Tensile Strengths Jl, J3.
Available with high-density polyethylene (Types II, III, IV) Class B and C (all colours).
Surface printed. Custom printing is available
Applications
Kynar/HMWPE: Cathodic Protection Cables, Primary Kynar Insulation, HMW (High Molecular Weight) Polyethylene Jacket. Stranded bare copper conductor conforms to ASTM Specification B-8. A homogeneous wall of natural PVDF fluoropolymer (Kynar) shall be extruded over the conductor.
An Insulation of high molecular weight polyethylene conforming to ASTM-D-1248, Type 1, Class A, Category 5, Grades E4 and E5. Tensile Strengths Jl, J3. Available with high-density polyethylene (Types II, III, IV) Class B and C (all colors). Surface printed. Custom printing available.
Application: A direct earth burial, DC lead, cathodic protection cable for use in deep anode groundbed installations, designed to withstand corrosive gases.
Halar v PVDF
Corrosion Protection Power supply units
Natural Air Cooled Rectifier
Australian Mining Product and Services supply Cathodic Protection Transformer Rectifier unit (TRUs) comprise of Automatic, Manual & CVCC controlled.
Cathodic Protection rectifiers are used for cathodic protection of plant facilities, buried pipelines, cross-country pipelines , storage tanks at terminals and other buried/submerged structures Our corrosion protection transformer-rectifier units are used to prevent submerged (Soil or water) metallic structures from corrosion.
All submerged Pipelines (Oil, water etc.), concrete structure of bridges/ buildings / sea ports etc can be protected from corrosion
Transformer rectification units impress DC Currents in to the Carbon-steel/steel structure to be protected in opposite direction to the galvanic corrosion currents & protects the structure from corrosion.
To obtain the highest level of protection under a variety conditions, it is imperative to vary the impressed current continuously so as to maintain a constant and steady level of protective potential at the structure. This continuous monitoring and control can be achieved by providing an automatic control for the cathodic protection system.
TYPES OF MODES
Auto Reference Mode
The operation of the TRUs in this mode will be fully Automatic and will be controlled by reference electrode feedback .The unit will automatically maintain reference voltage or P.S.P. of the set value under all conditions.
Manual Mode
The DC output voltage of TRU will be controlled in multiple symmetrical steps by means of a separate Auto/manual transformer with Coarse & Fine tapping.
CVCC Mode
The unit will be operated in Constant Voltage or Constant Current mode. In constant voltage mode the DC output voltage will be settable from 0 to rated value in stepless manner by means of voltage adjustable pot.
Corrosion Protection Tapes and coatings
PETROLATUM AND WAX TAPES
Application
This tape provides long-term corrosion protection to pipes, flanges, valves and related surfaces. Petrolatum tape that is designed to be used without a primer to protect dry, wet or submerged surfaces. The tapes provide long-term protection to pipes, pilings, risers, flanges, valves and related surfaces.
Petrolatum and Wax tapes pictured below:
HATCH SEALING AND HEAT SHRINK
Application
The function of hatch cover tapes is to protect the metal hatch covers on carriage ships against leakage of water into the carriage area. Extreme weather conditions often damage hatch covers making them prone to leakage which may lead to the damage of goods being shipped. Before applying the Hatch Cover Tape clean the surface to which it is to be applied thoroughly and make sure that the hatch cover is free of any salt from the sea-spray. The surface must be dry before tape application. In cold weather conditions use a torch to heat up the tape to achieve a better adhesive performance. Heat-shrink tubing is a shrinkable plastic tube used to insulate wires, providing abrasion resistance and environmental protection for stranded and solid wire conductors, connections, joints and terminals in electrical work most commonly.
Corrosion Protection measuring devices and instrumentation
DCVG EQUIPMENT
A direct current voltage gradient (DCVG) survey is a type of survey method that is used to assess the efficacy of corrosion protection, particularly on structures buried underground.
This is highly useful in the natural gas and oil industries, as this technique is used to trace coating faults as well as determine the deficits in the strategies that are used to control corrosion.
PORTABLE GAS DETECTORS
Portable Gas Detectors. The portable gas detectors supplied by AES can help you to detect toxic, flammable and combustible leaks, as well as monitor oxygen depletion. As they are
completely portable, these natural gas detectors can be handheld, clipped onto a belt to ensure that your space is monitored appropriately.
PIPE & CABLE LOCATORS
Undertaking any excavation will inevitably bring site workers into close proximity to underground utilities (electricity, gas, telecommunications, water). Consideration should always be given to knowing the exact location of all buried utilities before and during the excavation process.
To safeguard against utility strikes, a cable locator is used to detect the presence and proximity of buried utilities.
When an alternating current (AC) travels along a cable, an electromagnetic field is generated. The alternating current not only creates a magnetic field but also the oscillation of the current between positive and negative creates a frequency known as Hertz (Hz). The electromagnetic field generated by an AC current can be detected by a cable locator.
There are two main detection principles:
- Passive location– Used to locate an electromagnetic field already present on a utility
- Active location– Adds a specific signal using a signal transmitter onto a located utility
We manufacture and supply sites around Australia
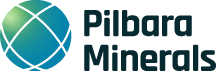
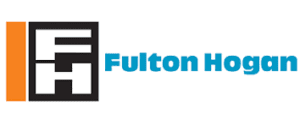
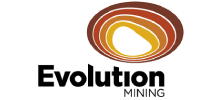
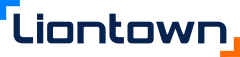
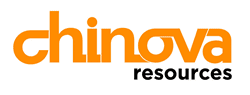
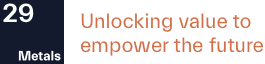


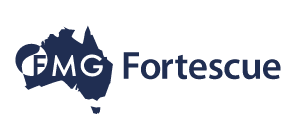
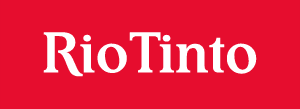