Linear Cushioned Vibrator
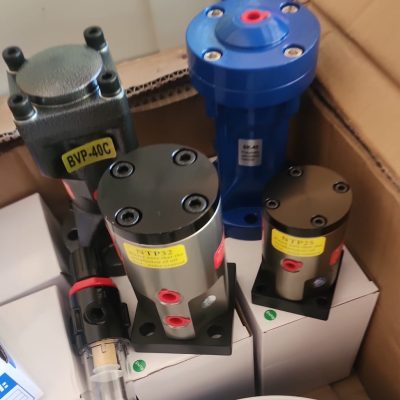
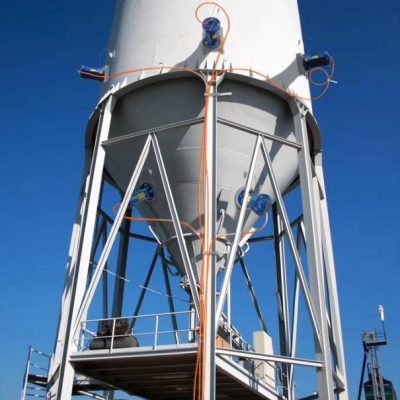

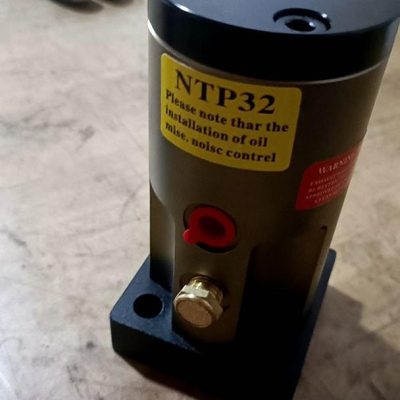
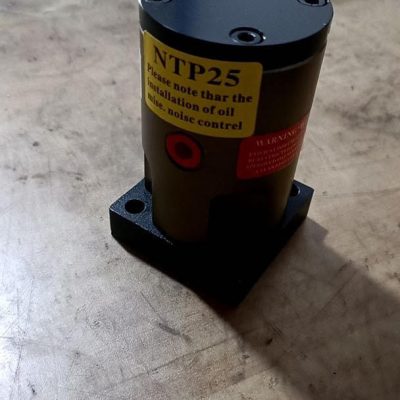
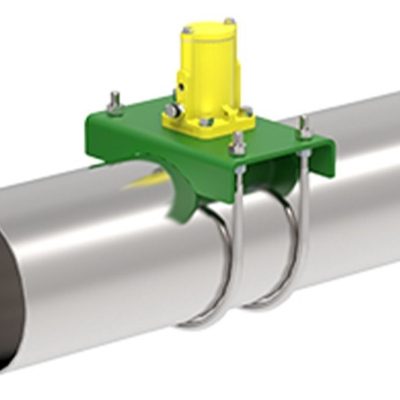
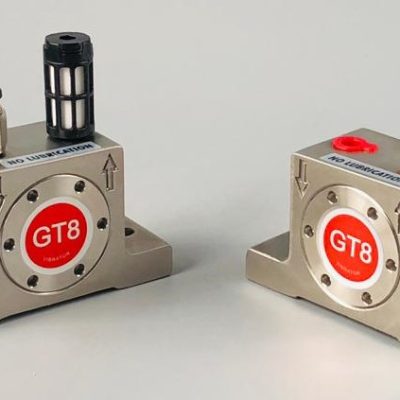
Keeping your product flowing, is critical – it determines the throughput
Material Flow issues are hard to deal with when a plant is operational and will disrupt operations costing both time and money, restricted material flow, hang up, carry back, and rat holding will occur in bins, hoppers, Dump trucks and wagons with pipes and chutes that carry material between transfer locations Industrial vibration is not just for those usual suspects; it can be just as successful when applied to those transfer chutes and pipes.
Our Bin, hopper pipe, truck or wagon Linear vibrators are designed to be easily installed, are pneumatic and safely aid any obstructed flow issues.
— We offer Vibrators that do not require the need to penetrate the wall of the vessel.
Our industrial Vibrators have been proven to aid the flow of material by reducing material hang-up problems ensuring bulk materials keep flowing in the toughest industrial
Notes On The Break-In Period For Drum Motors
There are a number of things to be aware of during the break-in period when new equipment is first used, usually referred to as the break-in period, in order to ensure that the equipment is used to good effect.
1. Leakage Occurs
Due to the looseness, vibration and heat of the drum motor parts, leaks can sometimes occur on the sealing surfaces and pipe joints of the equipment.
2. Fast Wear And Tear
Due to factors such as processing, assembly and commissioning of new equipment parts, sometimes the contact area of the mating surface is small and the permitted torque is large; therefore, the concave and convex parts of the surface of the drum motor are embedded and rubbed against each other during operation, so the metal debris from the grinding down will continue to participate in the friction as abrasive, which accelerates the wear of the mating surface of the parts.
3. Poor Lubrication
As the clearance of the newly assembled parts of the drum motor is small, then it is not easy for the lubricating oil to form a uniform oil film on the friction surface to prevent wear due to assembly and other reasons; this tends to reduce the lubrication efficiency, making the equipment cause early abnormal wear of the machine parts.
4. Looseness Occurs
Newly machined and assembled parts often have deviations in geometry and fitment size, and in the early stages of use the drum motor is subject to alternating loads such as shock, vibration and heat, deformation and other factors, as well as rapid wear and tear, which can easily loosen the original fastened parts.
By paying more attention to these aspects during the break-in period, problems can be identified and solved as early as possible, thus avoiding breakdowns in use and affecting the normal use of the equipment.
Request A Product Featured & Specification
We manufacture and supply sites around Australia
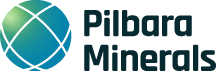
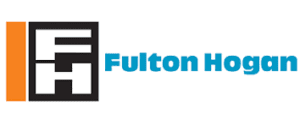
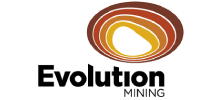
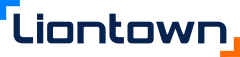
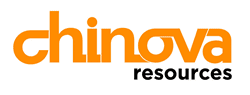
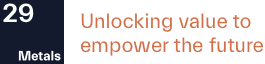


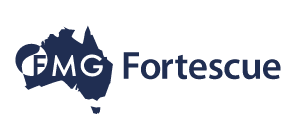
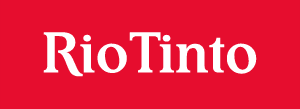