Free Asset Condition Report
Free asset condition report—with the ability to monitor wear to improve reliability
Asset Protection
Every process plant has a high reliance on its plant and equipment ( Assets ) The demand for increasing consistency and reliability of all sites equipment is determined by regular maintenance and a record of every asset
Asset management relies on a plant’s continuous maintenance and reliability activities with planning for refurbishments and replacements of equipment – as all plant and equipment have a definitive lift cycle and operational safety risk become more prevalent as its lifecycle draws to a conclusion
constant and clear reports on an asset will result in
- Better safety for personnel
- Provide input into replacements or refurbishments
- Guarantee throughput to enable budgetary requirements
- Reduce and highlight the risk
- Optimise energy requirements
- Better outcomes that ensure a higher degree of reliability
Plant Condition Assessment Guides Maintenance
ABSTRACT
1. THE ROLE AND IMPORTANCE OF CONDITION ASSESSMENT
Effective maintenance depends on a good knowledge of asset condition, which is achieved through regular condition assessment. Condition assessment identifies plant in sub-standard condition and hence at risk of failure, in turn allowing the efficient targeting of maintenance strategies. Condition assessments are also the basis for carrying out risk assessments.
Condition assessments of all types of assets, including process plants and structures, are performed throughout industry, and all involve the same basic objective and approach. Almost every company seems to have its own particular approach and checklists for recording information, despite the fact that all companies have the same objective in mind for the same equipment. Clearly, there is a case for some degree of basic standardisation in carrying out condition assessments.
National and industry standards and guidance for the inspection and testing of individual types of equipment and plant are widely published, but not on an inter-industry basis. Equipment manufacturers usually provide guidance on the condition assessment and monitoring of their equipment, to be included in maintenance programmes. Thus there is a rational basis for developing a more standardised approach for condition assessment between the various technical and national organisations.
Diversity of industry and of equipment type may have been viewed as obstacles to achieving a more unified or standardized approach to condition assessment in the past, but this can be largely overcome by adopting a flexible and common system of basic inspection formats covering all process plant. Another negative factor, perhaps, to a more unified approach is a lack of urgency, and hence of co-operation between various industry organisations and equipment manufacturers, to provide guidance and set the standards needed. This is changing, however.
Standardised approaches have been proposed and published in more recent years by industry associations for carrying out formal condition assessments [1– 10]. The objective appears to be the setting up of a standard framework or approach for carrying out condition assessment systems for particular industries, with guidance using suggested documented inspection checklists. For example, The Water Environmental Research Association [1], in collaboration with other organisations, identified the lack of standardised guidelines for conducting assessments, and prepared a document to address the situation.
The publications referred to discuss standard systems generally or very specifically. The purpose here is to propose a more standardised approach to the strategy and condition assessment of process plant of all types, using a staged approach in conjunction with standard assessment checklists. Standardised checklists allow the condition of plant to be quickly assessed by others, and the format design of such checklists is usually the result of considered evaluation by industry in general. The approach is illustrated in this paper via its application to process plant, but it can be applied to other engineering plant situations.
2. CONDITION ASSESSMENT METHODOLOGY
The standardised condition assessment approach proposed here for process plant can be viewed in broad terms as a staged process, as proposed in Figure 1 and described in Table 1. (Note: For simplicity, the hierarchical system used in this paper is: plant, unit, component).
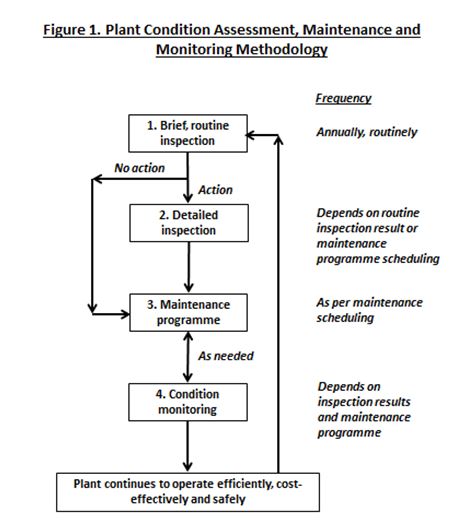
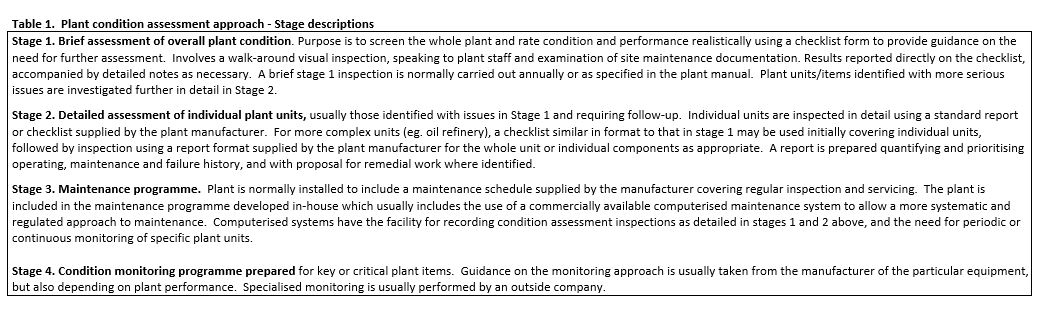
The various stages are linked through a unified system, starting with a brief, routine inspection and followed by a detailed inspection where warranted, both as precursors to setting up realistic maintenance and condition monitoring programmes. Standard checklists or inspection reports are proposed for the condition assessment in Stages 1 and 2, which can be universally applied to many plant situations. A single, basic checklist only would be needed for Stage 1 since this is a general assessment of a complete plant, looking at each type of unit collectively, e.g. groups of pumps performing similar functions. In the checklist, a particular property (e.g. visual condition) of a unit would be rated according to a scale.
For situations where more further detailed investigation is identified in Stage 1, or warranted through regulatory or standard practice requirements in more complex plant (e.g. steam turbines, process units in an oil refinery, etc.) a more detailed condition assessment would normally follow for the individual plant units (Stage 2). This would involve using standard checklists or reports for individual components (e.g. each pump) provided by the manufacturer of the plant itself or by a trade association. In the case of more complex plant (e.g. steam turbine) a detailed checklist might first be completed for the unit and sub-units, followed by a more detailed inspection report according to the manufacturer of the plant itself.
The checklists and reports proposed could be completed manually on paper or directly onto a tablet for subsequent downloading to a computerised maintenance system.
The point should be made that designing condition assessment forms for collecting information requires an understanding of human psychology if the reporting forms are to be completed fully and regularly. To this end, it is essential that they are as simple and effective as possible. Complex checklists are less likely to be filled in with any enthusiasm.
3. EXAMPLES OF PROPOSED CONDITION ASSESSMENT APPROACH.
The approach taken will depend on the type and complexity of the process plant being assessed. For example, the condition assessment of a simple water treatment plant using chlorine to disinfect borehole water would involve a Stage 1 condition assessment, and only a Stage 2 assessment where a serious deficiency is identified. In the case of an oil refinery or similar complex plant, say of a hazardous nature, and made up of various process units, a Stage 1 assessment would be carried out routinely, followed by a Stage 2 assessment of all units at longer time intervals. Each unit in an oil refinery (e.g. a desulphurisation unit) is as complex as a simple water treatment plant.
Two types of condition assessment reporting formats are proposed: a columnar checklist format in which a particular property is rated according to a scale (or a particular property value is stated) and an open report format where more detail is required in which a particular property value is stated or described. The practical application of both formats is discussed here.
A common use of a checklist in columnar format is to rate a plant unit according to a particular property, e.g. visual condition or performance. An overall rating for a single unit is calculated, allowing individual units to be prioritised for further action. A five-point rating system is proposed, following common practice in published references, and is described in Section 3.1. A columnar type format could also be used to state the value of a particular property. An open report format is commonly used where more detail is required, where the value of a particular property is stated.
3.1 Stage 1 condition assessment
The columnar type checklist format is appropriate in providing a simple but effective approach for a Stage 1 condition assessment. Table 2 shows an example of a Stage 1 condition assessment of a water pumping station, the operation of which is based on the abstraction and disinfection of water from boreholes.
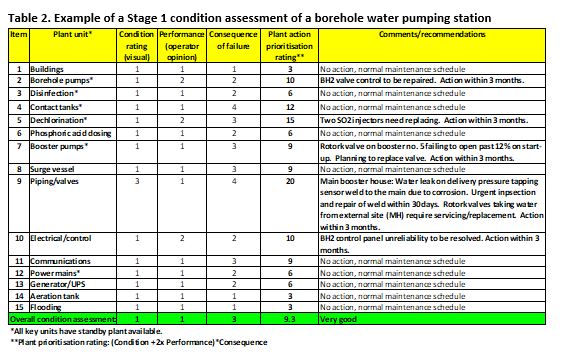
The inspection checklist format proposed in Table 2 would be a standard for all types of process plant, eg. power plants, refineries, water treatment plants. The plant unit headings would be appropriate to the plant being inspected, and be represented as a single category for units of similar service, ie. borehole, booster and high-lift pumps would be assessed separately in groups. Any additional issues specific to the plant in question which require further comment by the individual company itself would be contained in an appendix to the report.
In the example in Table 2, various deficient issues are identified and follow-up action proposed in order to rectify them through maintenance scheduling. Since the actions identified in this example are fairly straightforward in this case no detailed Stage 2 assessment is required.
3.2 Stage 2 condition assessment
A more detailed condition assessment (Stage 2) is carried out where this need is identified from the Stage 1 assessment, or as standard for more complex plant as warranted through regulatory or standard practice requirements, for example using inspection checklists or maintenance schedules prescribed by the manufacturer of the plant item itself.
An example of a detailed condition assessment report format for an individual unit, in this case a pump, is shown in Table 3. For more complex and hazardous plant, this assessment would sensibly be preceded using a more general columnar checklist covering all units or as appropriate (Table 4 column headings), followed by a more detailed inspection report for each unit or component where a deficiency has been identified (e.g. Table 3). Any additional issues specific to the plant in question which require further comment would be contained in an appendix to the report.
Table 3 Example of a checklist for the detailed inspection of an individual plant unit, in this case a pump (Stage 2). (Full checklist available from the British Pump Manufacturers’ Association [9])
Table 4 Suggested information to be included in a standard (Stage 2) report in columnar format for a unit or units in complex plant requiring more detailed condition assessment, e.g. a refinery desulphurisation unit.
(A separate detailed assessment would be completed for each individual unit or component as warranted, as per the format in Table 3).
The inspection checklist format proposed in Table 3 would be a standard for all types of process plant, e.g. power plants, refineries, water treatment plants. For complex plant, the approach might be to complete a brief, a Stage 1 condition assessment on a regular basis (say every six months) to provide a general idea of the plant condition (this would identify any urgent issues needing immediate attention), followed by a detailed assessment as in Tables 3 and 4 at a longer time interval.
4. A STANDARDISED CONDITION ASSESSMENT APPROACH
Condition assessment has always been a part of maintenance, but is often managed in a less coordinated or less systematic way than the standardised approach being advocated more recently here and in the literature. This comment also applies to the different condition assessment formats found in computerised maintenance management systems.
There are clear benefits in adopting a more standardised approach to plant condition assessments as suggested here: a clear, uniform presentation of essential data necessary to make an effective and balanced assessment, which allows inter-industry standardisation and hence comparison, and assists regulatory or inspection authorities in auditing company reports. The last is sometimes required by regulatory bodies, e.g. Ofwat, the UK water regulator.
The inspection checklist formats proposed in Stages 1 and 2 above are suggested, and final formats would be decided by broad consensus to cover all types of process plant. The ideal approach would be to have as few basic reporting formats as needed to cover most types of process plant situations. They should be designed to be as simple and effective as possible. A single brief, Stage 1 condition assessment checklist could be formatted to cover most process plant types. In the case of a Stage 2 condition assessment of complex plant reporting in more than one format may be advantageous for effectiveness, as appropriate. Again, the number of report formats could be reduced by careful selection of essential data to achieve as wide an application as possible.
For the condition assessment of individual units or components separate checklists or reports would be needed. These are mostly available from the unit or component manufacturers. Many process plants have their own peculiarities and hence operators would likely attach a brief, separate report to the standard checklist or inspection report to highlight specific issues.
It is suggested that a professional, trade or standards association would be the appropriate vehicle to organise the setting up and management of a standard plant condition assessment system. A committee comprising interested parties from engineering related bodies would be formed to advise and prepare the standard inspection checklists and reports, and associated documentation. This would provide a measure of confidence across industry in the soundness of the approach advocated and the documentation proposed.
References
1. Condition assessment strategies and protocols for water and wastewater utility assets. Water Environment Research Foundation (WERF), CSIRO, Australia. 2007. www.werf.org
2. Pump station condition assessments (a proven and defensible approach). Richards, M. and Greeley, P. Boston Water and Sewer Commission, USA. www.newea.org
3. Visual assessment manual for utility assets. New Zealand Water and Wastes Association, 2008. www.waternz.org.nz
4. Asset management condition grading standards. Saskatchewan Ministry of Municipal Affairs. 2006. www.saskatchewan.ca
5. Guidelines for condition assessments. Queensland Government, Australia. 2011. www.health.qld.gov.au
6. Condition assessment and asset performance guidelines. IPWEA-NAMS (Institute of Public Works Engineering Australasia-New Zealand Asset Management Support). 2007. www.ipwea.org.au
7. Development of health indices for asset condition assessment. Hjartarson, T., Jesus, B., and Hughes, D.T. Transmission and Distribution Conference and Exposition 2003, IEEE, USA.
8. Asset management planning. Portland Water Bureau, USA. 2013. www.portlandoregon.gov
9. Pump condition assessment template, British Pump Manufacturers’ Association. www.portlandoregon.gov http://www.portlandoregon.gov
10. Developing a quantitative method for assessing plant conditions. Qin Fen Zhang and Smith, B.T. (2013). HydroWorld.com.
Send us a message for more information regarding this service.
We manufacture and supply sites around Australia
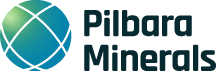
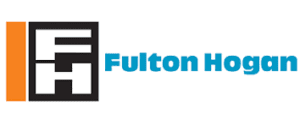
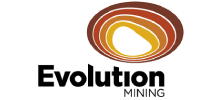
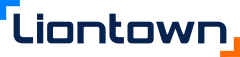
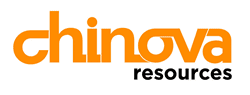
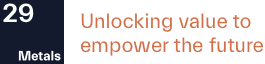


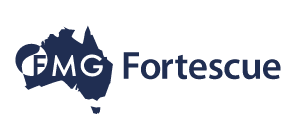
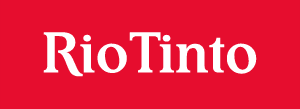